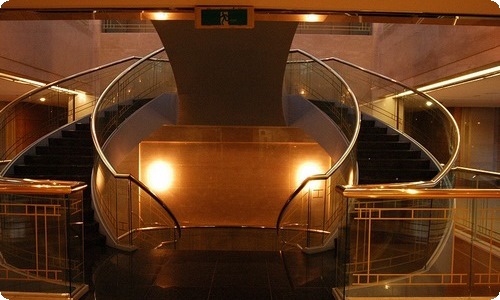
一、竞聘优势:
1、具有多年生产一线工作经历,及多年从事调度、生产计划工作,具有良好的协调、沟通和平衡能力,对现场生产、技术、设备情况比较了解,具备了良好的协调、沟通能力,有及时发现问题、解决问题的能力。
2、具有高度的敬业精神和责任意识。做事认真、踏实、努力、细心,能够全身心地投入到工作中去。
3、通过一年来的锻炼与学习,对熔铸厂铸锭加工工区各工序生产运行,计划排定,铸锭保供,安全质量,现场及人员管理,设备运行,工序配件,信息化等比较清楚,自认为能胜任熔铸厂铸锭加工工区副作业长工作。
二、工作成果:
1、制定了均热炉均火台账,合理排定均火计划,集中开动均热炉,缩短装炉时间,缩短均火间隔时间,减少电量及燃气量消耗,降低电、气单耗。连续均火5炉及以上排定均火计划,避免因长时间停炉后,在开动均热炉,冷炉均火增加一段升温时间,增加电量及燃气量消耗。全年共计节省电量292000kwh、燃气量109332m3,经济效益51.2万元。
2、老线均热炉圆铸锭均火转移,老线φ350及以上长根圆铸锭,由原来在104圆均热炉均火,转移至32t均热炉均火。改变装炉方式,缩短装炉时间,增加装炉量,减少耗电量,降低电单耗。老线104圆均热炉为立式装炉,因装炉过程中铸锭惯性摆动,在摆动过程中碰撞炉内护板,对炉体及电阻带造成损坏,并且装炉时天车工视线不好,增加装炉时间,炉温损失较大,增加了下炉均火升温时间(每炉均火升温时间在14小时以上),增加耗电量。32t均热炉为推进式装炉,同比104圆均热炉每炉可缩短装炉时间50分钟以上,同比104圆均热炉均火升温时间每炉减少2小时。老线φ482规格圆铸锭在104圆均热炉均火一炉最多装6根,通过对32t均热炉均火料架进行改良,32t均热炉φ482规格圆铸锭,一炉最大装炉量为9根,同比104圆均热炉多装3根。通过测试老线104均热炉同比32t均热炉耗电量大、电单耗较高。用相同制品、相同均火时间、相同装炉量进行测试,104均热炉平均一炉耗电量12000kwh、电单耗429kwh/t;32t均热炉平均一炉耗电量8800kwh、电单耗314kwh/t。老线104均热炉同比32t均热炉每炉耗电量3200kwh。全年共计节省电量1144800kwh,经济效益68.6万元。
3、缩短北线均热炉出装炉时间,实现提前备料,降低炉温流失,对北线均热炉出料台及托盘进行改造,使其与各台炉子实现通用。改进2#均火炉炉门水管位置,防止3#和4#炉备料装炉时刮蹭。在改造后的两托盘上加装硬限位,防止备料时料盘串动。修复新长光加料车,使两台加料车能够同时具备备料和出装炉作业条件。将112#天车由驾操作改为地操,减少驾控人员占用,便于地面操作。北线均热炉改造,自5月份开始实现提前备料,出装炉时间从原来3-4小时,降低至0.5-1小时,大幅度缩短了装炉时间,平均月均火量同比增减291t,降低炉温损失,共计节省电量117211kwh,天然气81499m3,经济效益38.3万元。
自2019年7月份调任铸锭加工工区副作业长以来:
1、生产效率方面:研究制定合理有效率生产流程方案,制定有效合理的奖罚机制,实现铸锭按合金系及规格分组、批量加工,减少锯床因频繁更换规格调整参数,减少铣床因频繁更换合金调整角度,最大限度提升北线锯床、铣床生产生产能力。从原来的锯床班产10-18块,铣床班产5-8块,至现今锯床班产最低25-42块,铣床班产 11-17块。2020年,北锯日产最高107块,北铣日产最高45块,日发送最高98块。2020年6月份,北锯通过量23878t,北铣通过量7477t,创造了建线以来最高值,最大限度提升了北锯、北铣生产效能。制定圆铸锭生产日计划,圆铸锭特点多品种、多规格,加工过程易混乱,增加员工重复作业及工序重复操作。合理排定圆铸锭班、日生产计划,从来料、均火、机加实现整熔次加工,最大限度减少员工重复作业,工序重复操作,提高圆机加生产效能及铸锭保供能力。
2、质量管理方面:为了减少铣面后铸锭表面与吊具,在吊运中造成磕碰伤,影响下到工序,对现场吊钳进行改造及包护,将吊钳下方与铸锭接触面处用尼绒布包护,或更换尼绒辊,避免吊钳下方硬铁与铸锭表面接触造成磕碰伤,实施后达到了非常有效的效果。
结合加工分厂质量需求,根据所生产合金特性,制定铣面优质操作法。1、3系等软合金表面粘刀痕现象,根据来料厚度,适当调整进刀量,铣大面时分3刀铣面,根据来料厚度第一刀进刀量小于9mm,速度选择小于1600mm通过,第二道及最后一刀根据铣面要求平均分配进刀量,第二刀速度3200mm通过,最后一刀速度3200mm通过,并做最后光洁面调整,通过上述操作法有效解决了1、3系合金铣面后表面粘刀现象。
2、7系等硬合金大小面交角处加工毛刺现象,定期调整主铣头粗刀内八刀和外八刀,半精刀及精刀之间高度差,缩短半精刀与精刀之间高度差,增加半精刀铣面负担,降低精刀铣面负担,最终减少出刀侧加工毛刺。通过上述操作法有效解决了2、7系合金铣面后大小面交角处加工毛刺现象。
3、区域建设方面:重新制定了工区各项岗位职责、安全职责、管理规定及办法,共计12项。
4、现场管理方面:对现场进行合理区域划分,规范物料及必须品定置摆放,定期处理废旧物品,划分区域负责人,每班次进行现场清理,达到现场规范化管理,每日进行自检,检查不合格项参与班组绩效考核,2019年7月份至今,通过区域员工共同努力,北线锯、铣床现场达到了翻天覆地的变化。
三、不足之处:
1、一些工作做的不够细致,缺乏科学的管理;
2、有时候在工作中方式方法不够灵活;
3、性格中仍未克服急躁的缺点。
四、2020年下半年工作计划:
1、北线锯床、铣床上、下料储料平台改造、延长,增加待加工铸锭储备能力。北线锯床生产线现有操作人员3人,分别为:操作手1人、上料区地操天车1人、下料区地操天车1人。北线铣床现有操作人员2人,分别为:操作手1人、天车协作1人。承担锯切、铣面、各熔铸车间及各加工分厂的铸锭接收与发送、废料收集及发送等工作,班产量20-25块。由于生产任务量逐年增多,及辅助工作任务增加,导致人员匮乏。北线锯床现有上、下料储料平台,只能满足准备3块铸锭能力,北线铣床无上、下料储料平台,导致地操人员频繁操作天车吊运料。通过对储料平台进行升级改造,延长储料平台及行走小车行程,实现上、下料平台具备储备6-8块铸锭能力。缩短上、下料岗位吊运时间,节省人力资源,提高辅助工作效率,提升铸锭发送与保供能力。储料台储备能力增加,缩短生产辅助时间,提升锯切进度,班产量预计可提升至30-35块铸锭。
2、细化圆铸锭生产计划及在制品台账管理,结合加工分厂铸锭保供及质量需求,生产及设备实际情况分析,员工劳动强度分配,减少工序重复操作等方面入手,从班计划到日计划再到周计划,实现在制品心中有数,加工进度时时跟踪,彻底实现从进到出整熔次加工。
各位领导,各位评委老师,以上为我本次竞聘报告。